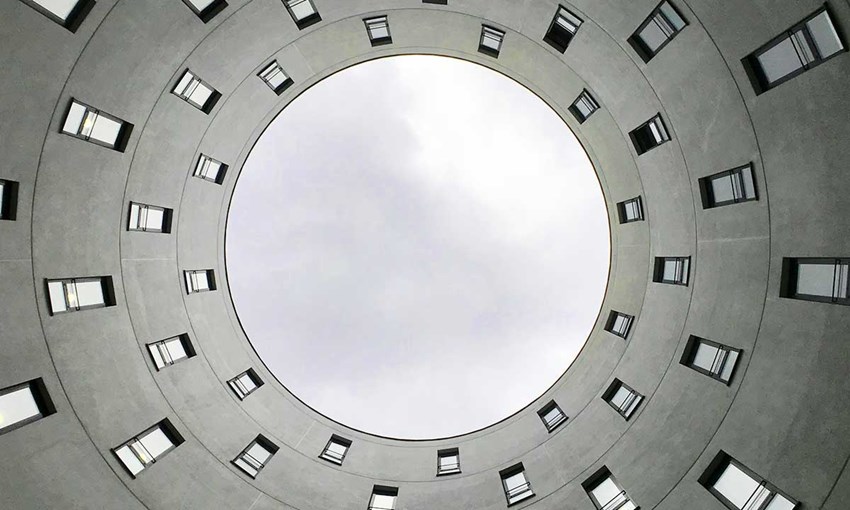
Ok. So...
Generally speaking, there are three main phases of a building project. But we need to sort out a quick thing before we dive into them...
The project scope is the red thread through the phases
Every building project is initiated by someone. And the funds need to come out of someone's pocket. This "someone" is the client. This could either be a person, a public entity, or a private firm. Regardless of who it is, the client tends to set the project's tone and appoint experts to bring it to fruition. Get to know the client better >
The client's wishes, demands, and expectations are translated into a project scope. In simplified terms, a project scope is a written statement describing the vision, goals, and work needed in a construction project. It's typically also where a critical decision is made: whether to use BIM (keep in mind that BIM is a requirement for public procurements in some nations) or go old-school.
Building phase 1: Design and selection
This creative phase of the process starts with the designers (architects, engineers, and interior designers) feeding off the client’s concept and demands. The scope is set, and it’s on the designer’s table to unite the performance demands with their creative vision and aesthetic flair. The design phase in a digital construction project normally consists of three main steps:
- Concept design
- Data input
- Showing the 3D model to the client
But let’s bounce back to the part about "performance demands" and "data input":
The importance of data in construction is seeping down to the early stages of a project. Designers need to scrutinize product geometry and performance data in order to select components that align with the goals of the building project. This means that a window is no longer “just a window” – it’s a building component that plays a part in the building’s overall thermal transmittance, natural light, and life cycle.
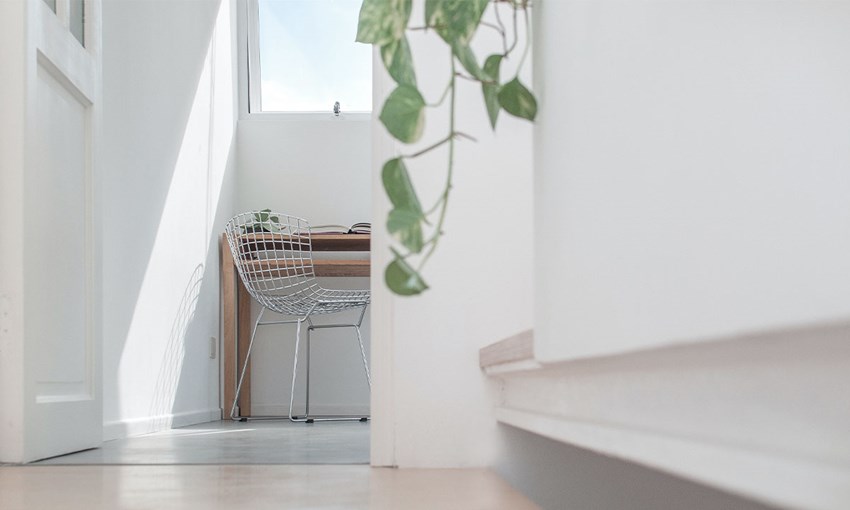
Psst! Did you know that we've partnered up with Prodikt to provide a smooth and easy way to get sustainability data on products? Now you do – read all about the sustainability platform >
The phase can be a rather complicated and time-consuming hunt for information. But with BIM – and BIM objects – product selection, ease of shared information, and greater data accuracy make it easy. The ability to collaborate digitally, with all players able to access, discuss and amend data and aesthetics, simplifies the process, boosts accuracy, and cuts out errors upfront.
Why the design phase is crucial for manufacturers
Manufacturers create products. Once made, you’ve got to sell it. Manufacturers need to turn into marketers magically, and getting on a specifier’s list is the golden rule. How can you do that? Well, given that you’re 80% of specifications are based on the design (DBEI), the design stage in a construction project is a critical time for future business.
See, manufacturers who offer information early on will reap the benefits later. Designers want BIM objects for a smoother product selection and design process. If you could save time and influence the decision-making process, and therefore engineer a faster route to specification, you would, wouldn’t you?
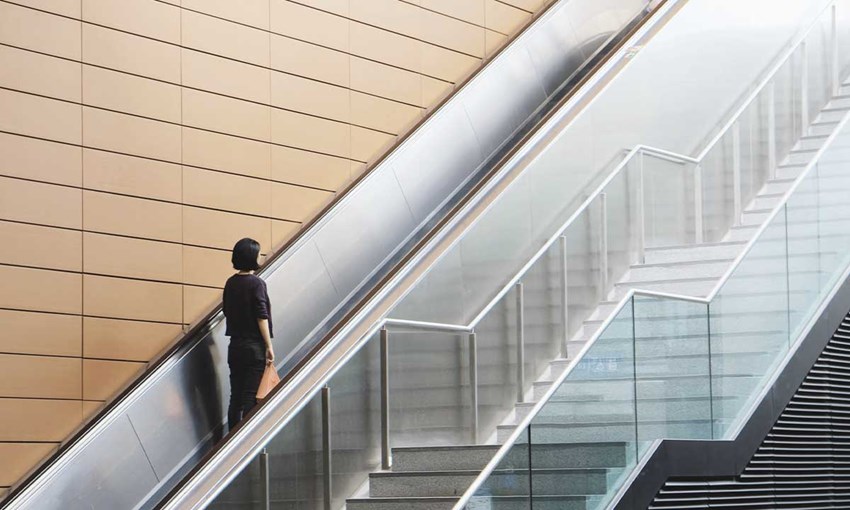
Thought so.
As with all things related to outreach, there are BIM marketing methods to employ. But you need to establish the foundation before you build up and reach out. Putting your products on BIM and BIMobject gives manufacturers a ready-made marketplace to reach, understand and influence specifiers. Correctly done, you'll give designers, engineers, and architects an easy route to include your products in the BIM model and influence the final purchase.
Phase 2: Build
That’s right, you guessed it: it’s time to build. After the design has been signed, sealed, and delivered, the long building process awaits! Concrete needs to be set, screws need tightening, and building products need to be delivered exactly when they're needed. Multiple moving parts make timing, planning, professionals, and logistics crucial for project success. Generally speaking, there are four steps within this phase:
- Setting the work plan.
- Keeping track of time and costs.
- Delivering and receiving materials.
- Construction.
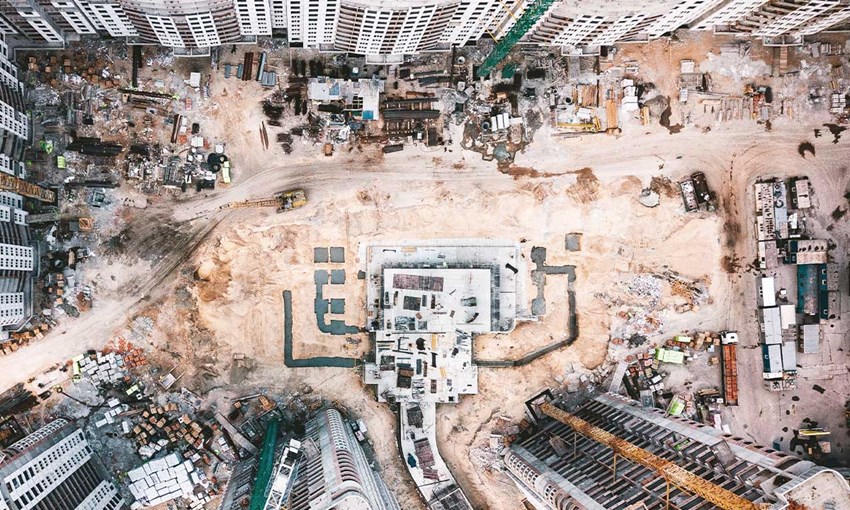
It's an exciting phase of any project. But it's also rife with risks ranging from insufficient product installation documentation to uncoordinated deliveries. Basically: a lack of information hikes up costs and construction waste. But how can construction professionals put a stop to the inefficiency? Matteo Santi, BIM coordinator and MEP coordinator at Gianni Benvenuto S.p.A, shares his solution in a recent interview:
“The use of BIM software within the construction process of complex buildings and imposing dimensions has become indispensable. In particular, the coordination and management of information can lead to a significant reduction in construction time and efficient coordination of workers on the construction site.”
So, how can you facilitate a smoother construction phase and build better relationships with construction professionals? And why does it even matter? Let's dive into it:
Connecting with construction teams is crucial
We mentioned the importance of manufacturers collaborating with all players in the design phase. But it’s equally vital to connect and work with all stakeholders. And that includes construction teams. After all, contractors typically place orders, and the construction workers install your products. So, you need to provide them with the product information they need to put the pieces together and form the whole.
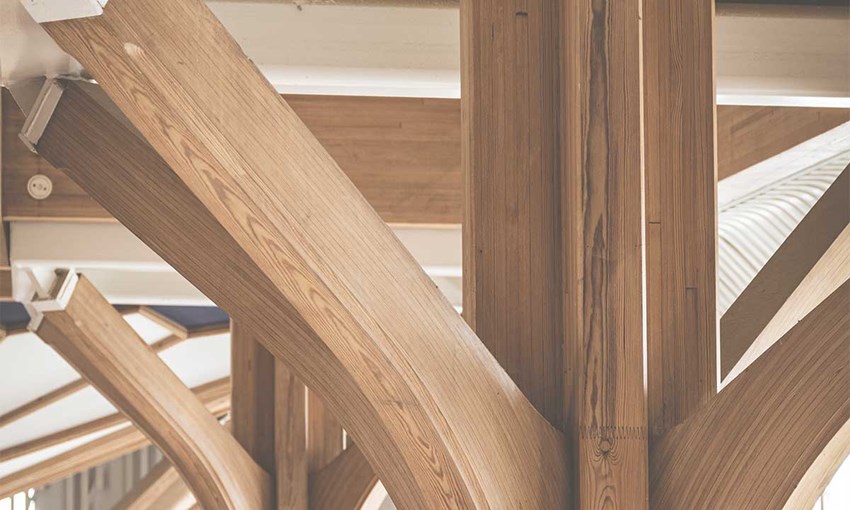
Matteo stated that coordination and management of information lead to greater productivity. But how? Well, it all boils down to the visualization capabilities and open access to project information offered with BIM. Access to full data, visuals, and specifics is what all stakeholders crave.
Manufacturers who supply BIM objects facilitate smooth operations and a timely process. And that added value is something your customers won't forget when it's time to move on to the next project.
Phase 3: Maintaining the built asset
Designed, planned, and built. And you’re done! Well, not quite. Actually, far from it. After a building's erected, it needs a bit of maintenance work to keep it in tip-top shape for as long as possible. Collaboration (there’s that word again) through BIM with the facilities and other maintenance teams will be important over the coming months, years, or *fingers crossed* centuries.
Let's harp a bit on why it's important to maintain existing structures. One part is, of course, keeping operational costs down. But another part is renovating and updating structures to net-zero carbon standards. Here's why it matters:
- Global average renovation rates must increase from 1% to 3% if we are to meet the Paris Agreement’s 2050 net-zero carbon goal (The World Green Building Council).
- A 2019 study by Rob Marsh states that prolonging a building’s lifespan from the rough average of 50 years to 120 years will reduce its environmental impact by 44%.
- To make sure you have control of your carbon data from start to finish, check out what Prodikt can do for your building projects.
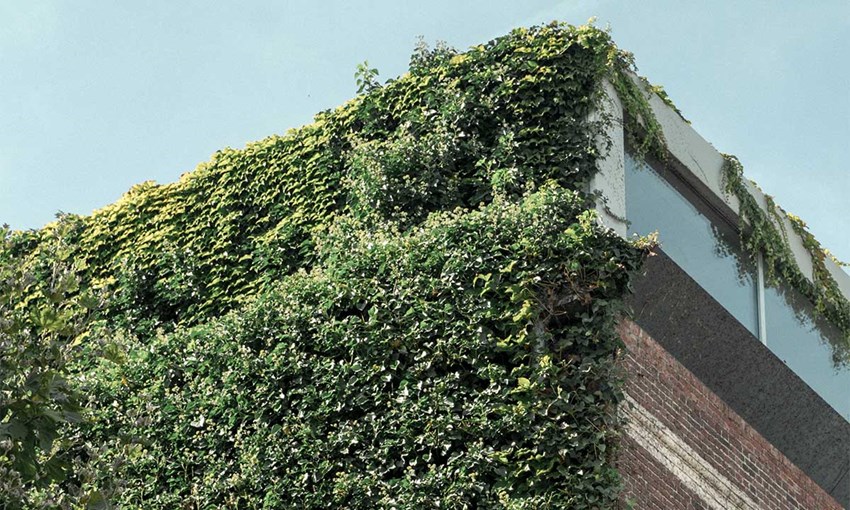
Want more numbers and green insights? Get your copy of Why sustainability is key to getting specified today!
How to maintain relationships after installation
You see, as a manufacturer, if you’ve implemented the right data from the start, a building operator will have an abundance of useful information to optimize energy performance, run maintenance testing on products, predict future maintenance costs and set up programs.
And as products near their expiration date, manufacturers should be primed to work with partners to propose updates, add-ons, maintenance, or new solutions as your products approach their expiration date.
Although there are a lot of things to do to keep the wrecking ball from swinging, chances are that it'll happen someday. But how can BIM be of assistance? A BIM building contains heaps of project and product data. This makes it easier to extract exact material and volume information as well as integrate the information for detailed waste estimation, planning, and recycling.
We've come full circle and full service.
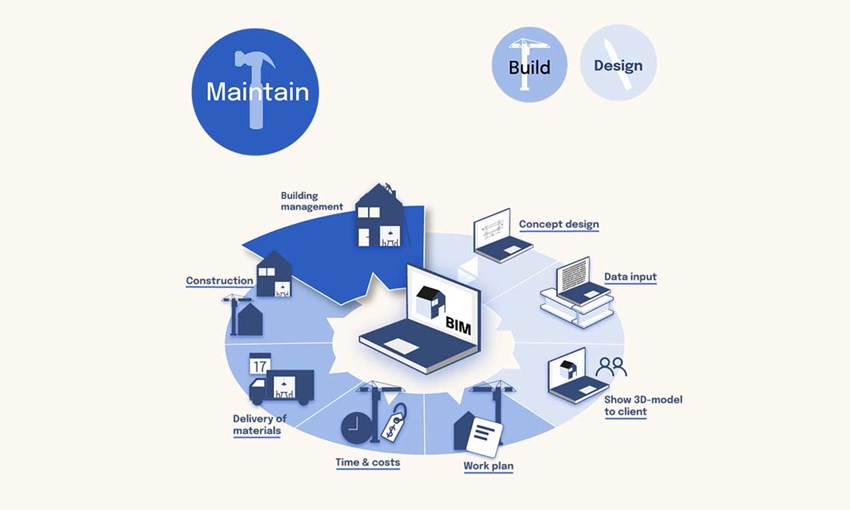
Want to get nitty-gritty with the phases of a construction project? Or become a master on how to collaborate through them all? If you nodded your head once or twice, you should...
Sarah Chase
Global Content Marketer